The process of making a masterbatch begins with the weighing of the ingredients. The toner, carrier, and lubricant are weighed separately and the weights need to be accurate. These materials are put into a mixer and mixed well. They are then subjected to heat or extrusion. The mixture is then allowed to cool and granulated. The final masterbatch is then packaged according to customer requirements.
This process can be done by wet or dry production. In wet production, a mixture of water and solvent is used to disperse the pigments superfine. In dry production, the pigments are dissolved in an organic or inorganic solvent. The resulting solution is called a color masterbatch or pigment dispersion. In the manufacturing process, a two-roll plasticizer is used to mix the dispersion with the polymer. The result is a pelletized pigment.
There are various types of masterbatches that can be manufactured, depending on the product type, substrate type, and state of the product. Solid masterbatches are the largest segment of the global masterbatch market and are mainly made up of pigments and additives bonded to a compatible carrier material. They are widely used in the automotive, consumer goods, electronics, and construction industries. Some of the major companies that offer solid masterbatches include Ampacet, Avient, Penn Color, and Sukano.
Liquid masterbatches are the second-largest segment of the global masterbatch market and include a wide range of specialty chemicals that enhance the performance of plastic products. These are usually added to a base polymer in order to impart durability, improved electrical and thermal properties, enhanced UV protection, or anti-fungal and bacteria-resistant properties. The major liquid masterbatches are surfactants, polymer extenders, and polymer stabilizers.
The global masterbatch market is primarily driven by the demand for sustainable solutions, as most manufacturers are moving away from petroleum-based additives. Moreover, growing economies such as India and China are increasing the adoption rate of masterbatches. This is leading to significant investments in R&D by players. Furthermore, the rising demand for sustainable masterbatches in the automotive sector is expected to propel the market. This is owing to the fact that these masterbatches offer better wear and tear resistance, higher flexibility, and improved chemical stability. The increasing awareness about environmental issues is influencing the consumers to adopt these eco-friendly additives. The growing demand for masterbatches is also boosting the overall market for plastics, as these additives help in the fabrication of durable products with enhanced quality and aesthetics.
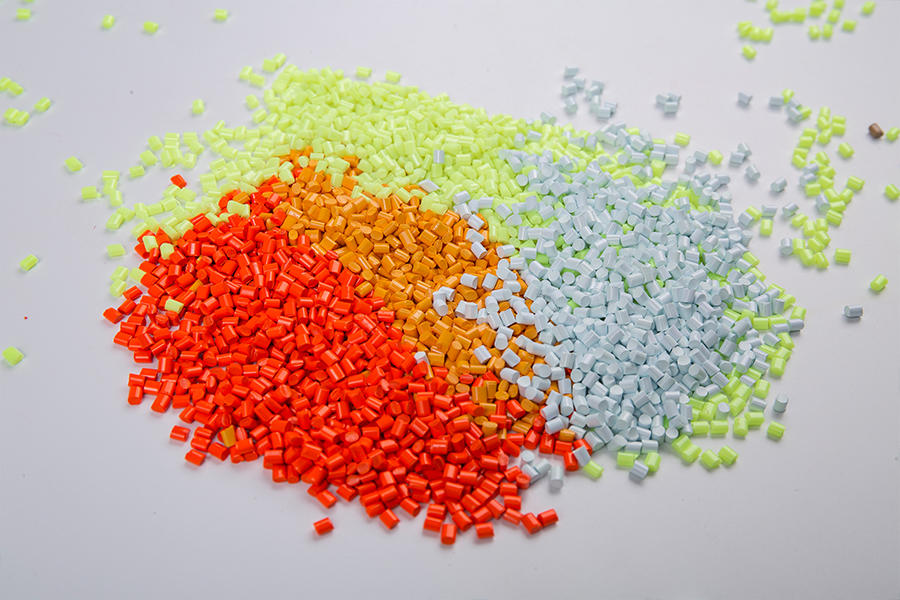