In the dynamic realm of plastic manufacturing, the masterbatch factory stands as a cornerstone of innovation and precision. These facilities play a pivotal role in the creation of colored and functional plastics, providing the industry with the essential pigments and additives that define the visual and performance characteristics of a vast array of products.
Masterbatch factories are equipped with state-of-the-art machinery and technology designed for precision and efficiency. The manufacturing process typically involves the meticulous blending of pigments or additives with a carrier resin to create a concentrated and uniform masterbatch. These masterbatches, available in pellet form, serve as the building blocks for achieving specific colors or functional properties in the final plastic product.
One of the distinctive features of masterbatch factories is their ability to customize formulations to meet the unique needs of clients. Whether a manufacturer requires a specific color for branding purposes or a particular functionality, masterbatch factories collaborate closely with clients to create tailor-made solutions. This customization capability ensures that the final plastic product not only meets technical requirements but also aligns with the aesthetic and functional goals of the end user.
Maintaining a stringent quality control process is paramount in the production of masterbatches. From raw material selection to the final pellet output, masterbatch factories implement rigorous testing protocols to guarantee consistency and reliability. This commitment to quality assurance is crucial for manufacturers relying on masterbatches to achieve precise color matching and performance characteristics in their end products.
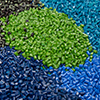