A common example of a raw material is iron ore. The raw material is embedded in rock formations, and it is mined for its metallic content. The metal is then put through a smelting process to remove the oxygen, leaving behind pure iron. The resulting metal is the raw material that is used in construction and manufacturing.
Companies often require a rigorous selection and testing process for raw material suppliers. This is not only due to food safety regulations, but also to ensure that the supplier will consistently deliver high quality raw ingredients. This is done by assessing general supplier information, as well as analyzing a sample of the raw material against the company’s specific quality standards and guidelines.
It is important to remember that the raw materials will eventually become the finished goods and are therefore critical to the quality of the final product. Poor-quality raw materials will inevitably produce low-quality finished products, leading to customer dissatisfaction and complaints. In addition, a poorly-designed or executed raw material management process can cost the company money and time.
Having accurate raw material consumption data is essential to effectively managing the production cycle and making sure that your company does not overspend on materials. This can be achieved by implementing a system that monitors consumption and automatically updates the inventory level. In order to ensure the accuracy of this system, it is a good idea to conduct periodic reviews and make changes to improve it.
A company’s raw material inventory is a significant portion of its total inventory, and it’s therefore important to take care to manage it carefully. For example, it’s a good idea to have a clearly defined inventory policy and set policies for purchasing and receiving raw materials. Additionally, it’s important to have a designated materials manager who is responsible for the entire process. This will help ensure that the company’s policies are being followed and reduce mistakes.
In order to avoid costly inventory errors, it’s also a good idea to start with basic raw material inventory tracking and only increase its complexity when there is a clear need for it. Finally, it’s a good idea to consider getting technological help if necessary to automate and streamline the raw materials management process. This can include everything from calculating the raw materials consumption formula to producing reports and monitoring inventory levels. This can help ensure that the raw materials are always in the right place at the right time, which is essential to ensuring that your company can meet customer demand.
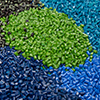