PET masterbatch is a concentrated mixture of pigments or additives encapsulated in a carrier resin. This carrier resin is typically made of the same polymer as the final plastic product, in this case, PET. The masterbatch is then introduced into the plastic manufacturing process to impart color, modify physical properties, or achieve specific performance characteristics in the finished plastic goods.
The production of PET masterbatch involves the dispersion of pigments or additives in a carrier resin using specialized equipment. The mixture is then pelletized to create small, uniform pellets of concentrated color or functional additives. The resulting PET masterbatch is convenient for handling, transportation, and easy incorporation into the plastic manufacturing process. Manufacturers can customize masterbatch formulations based on specific requirements, allowing for a broad spectrum of colors and performance enhancements.
One of the primary applications of PET masterbatch is in providing vibrant and consistent coloration to PET plastics. Whether it's packaging materials, containers, fibers, or other PET-based products, masterbatch allows manufacturers to achieve a wide range of colors with precision and uniformity. This ensures that the final plastic products not only meet aesthetic expectations but also adhere to brand identity and market trends.
PET masterbatch offers significant advantages in terms of processing efficiency during plastic manufacturing. The concentrated form of color or additives simplifies the blending process, reducing the likelihood of color inconsistencies and streamlining production. The ease of handling and incorporation into the production process also contributes to increased efficiency, reducing manufacturing time and costs.
Beyond coloration, PET masterbatch is employed to introduce functional additives into PET plastics, enhancing their performance. This can include additives such as UV stabilizers, anti-static agents, flame retardants, and more. These additives address specific requirements such as improved durability, resistance to environmental factors, or compliance with regulatory standards, making PET masterbatch a versatile solution for various applications.
As sustainability becomes a focal point in the plastics industry, PET masterbatch manufacturers are also exploring eco-friendly alternatives. Bio-based carrier resins and pigments derived from natural sources are being incorporated into masterbatch formulations to reduce the environmental impact of plastic products. This aligns with the industry's efforts to create more sustainable and recyclable materials.
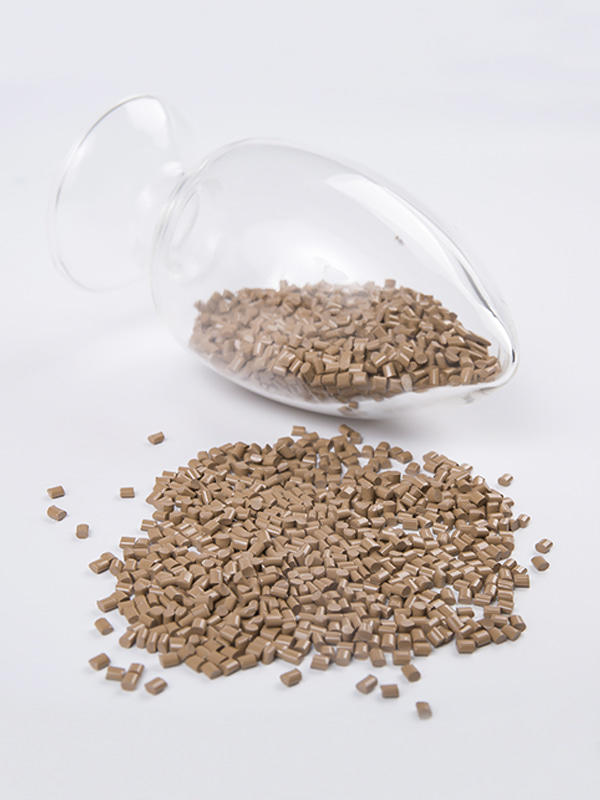