Plastic fiber masterbatch has emerged as a pioneering solution in the world of plastic manufacturing, revolutionizing the way synthetic fibers are incorporated into various products. This additive, a concentrated blend of materials, is designed to reinforce plastic fibers, imparting enhanced strength, durability, and performance to a wide array of applications. In this article, we will explore the significance of plastic fiber masterbatch, its manufacturing process, and the transformative impact it has on the strength and versatility of plastic-based materials.
Plastic fiber masterbatch is a specialized formulation created by combining reinforcing fibers with a carrier resin, often made of the same polymer as the final plastic product. These masterbatches are introduced into the plastic manufacturing process to enhance the physical properties of the resulting fibers. The reinforcing fibers can vary in type, including glass fibers, carbon fibers, or aramid fibers, each offering unique characteristics to improve the overall strength and durability of the plastic.
The production of plastic fiber masterbatch involves the encapsulation of reinforcing fibers within a carrier resin through specialized compounding equipment. The mixture is then pelletized, resulting in uniform and concentrated pellets that can be easily integrated into the plastic manufacturing process. The versatility of this masterbatch allows manufacturers to tailor formulations to meet specific strength and performance requirements for diverse applications.
The primary benefit of plastic fiber masterbatch lies in its ability to significantly enhance the strength and durability of plastic products. When incorporated into plastic fibers, these reinforcing additives create a composite material with improved tensile strength, impact resistance, and overall structural integrity. This makes plastic fibers fortified with masterbatch ideal for a wide range of applications, including automotive components, construction materials, and consumer goods.
Plastic fiber masterbatch's versatility extends to a myriad of applications where enhanced strength and durability are essential. In the automotive industry, these reinforced plastic fibers contribute to the production of lightweight yet sturdy components, aiding in fuel efficiency and overall vehicle performance. In construction, the use of masterbatch in plastic fibers strengthens materials, increasing their resilience to harsh environmental conditions. Additionally, consumer goods such as sports equipment, household items, and electronic devices benefit from the improved durability offered by plastic fiber masterbatch.
One of the key advantages of plastic fiber masterbatch is its adaptability to meet industry-specific needs. Manufacturers can customize masterbatch formulations to achieve specific performance characteristics required for diverse applications. Whether it's increased temperature resistance, enhanced flame retardancy, or specific mechanical properties, plastic fiber masterbatch allows for precise tailoring to meet the unique demands of various industries.
As sustainability becomes a focal point in material science, plastic fiber masterbatch manufacturers are exploring eco-friendly alternatives. The development of masterbatches with bio-based carrier resins or recycled reinforcing fibers aligns with the industry's commitment to reducing the environmental impact of plastic-based materials.
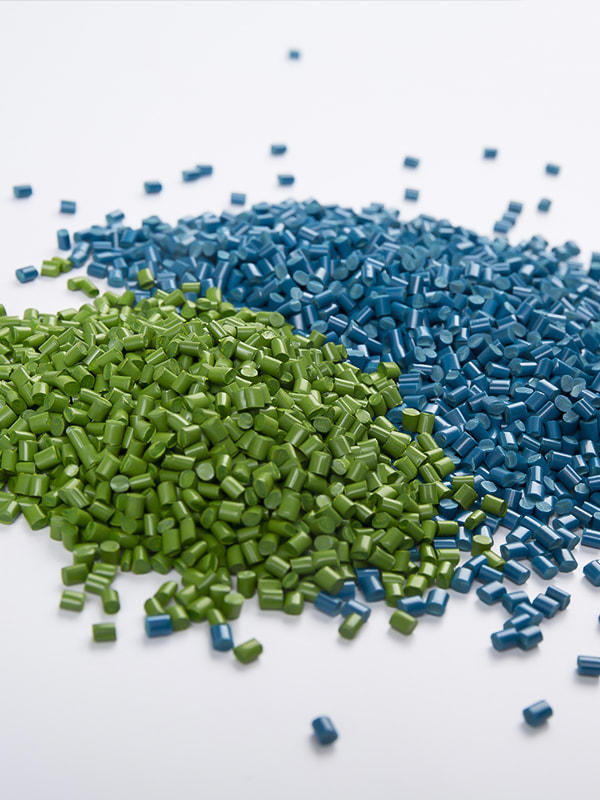